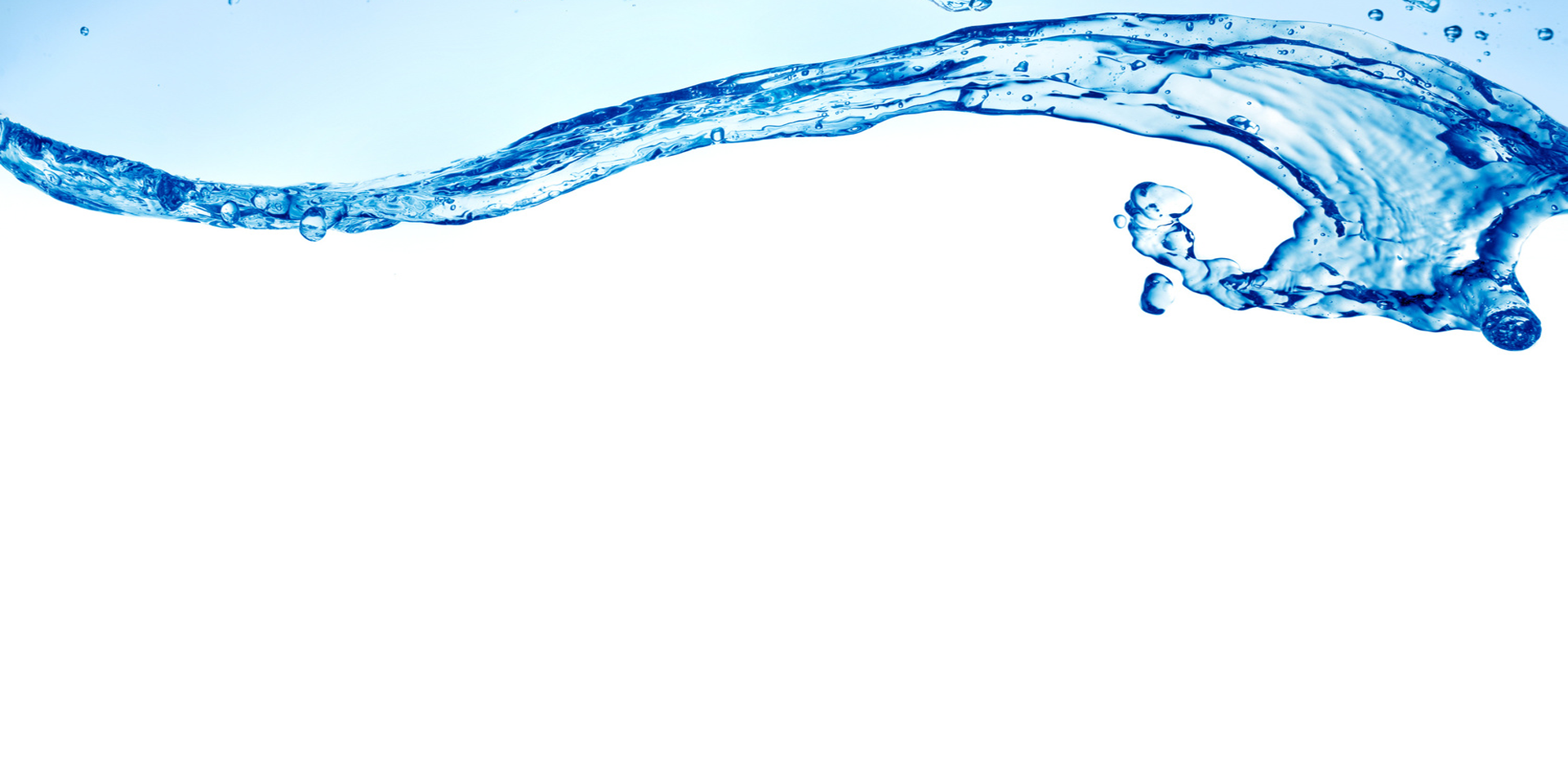
Candle filters
The candle filter is not only used in beet sugar factories but also in sugar refineries and sugar cane factories. The pressure filter systems are a perfect solution for thickening of suspensions with low to moderate solid contents, particularly for syrup filtration, sugar liquor, PAC system. The filters are used successfully in sugar beet factories as well as in sugar refineries. Application in sugar cane factories is also possible. These low pressure filter systems are particularly suitable for thickening of slurries with low to moderate solid contents, for safety filtration and for syrup filtration.
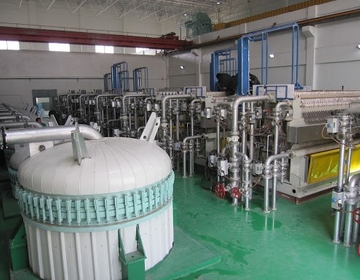
- for filtration of carbonated juice after the first and the second carbonation
- As safety filters for thin juice for fine filtration of syrups with the addition of filter aids.
- for thickening of carbonated clarified liquor Advantages of candle filters:
- Programmable control ensures fully automated operation
- Thickening rate is individually adjustable (depending on application up to 650 g/l)
- No additional energy required for cleaning
- Durable equipment
- Sturdy filter elements
- High specific throughput rate because of short cycle times
- Quick exchange of complete intermediate bottom complete with filter candles if needed
- CIP (cleaning in place) of filter cloths in closed candle filter to extend cycle times before exchange (option)
FILTRATION AND SUGAR LIQUORS
The filter consists of a cylindrical body 1 with a spherical lid 2. The body houses radial filtration frames 3. The non-filtered product is fed through an inlet 4. The filtrate is removed through an outlet 5. The slurry concentrate is removed from a cone bottom part of the filter through an outlet 6. The thickening filter (hereinafter – filter) is designed for filtration of juices in processing sugar beet, and raw sugar re-melts with generation of the filtrate and slurry concentrate.
The filter is a part of a filtration station consisting of several filters and equipped with an automatic control system for monitoring the filtration process Quality.
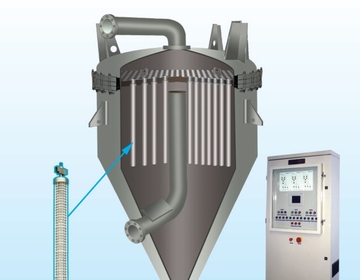
SUGAR LIQUOR FILTRATION
Thick juice leaving the evaporation station and sulfitated re-melts at refineries processing cane raw sugar can also be filtered by these thickening filters. The filtrate, i.e. filtrated syrup, goes to a standard syrup mixer. The filtration media is filter cloth, and the filtering layer is a layer of perlite mixed with the unfiltered sugar liquor in a ratio, which determines a filtering surface area of the filter.
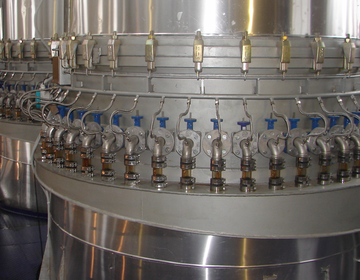
- Filtration rate:
- 1st carbonation slurry up to 1.2 m3/m2
- 2nd carbonation slurry up to 1.8 m3/m2
- Guaranteed filtrate quality:
- 1st carbonation slurry 10 ppm
- 2nd carbonation slurry 7 ppm
- Filter body material grade St3sp (non-alloy quality structural steel)
- Filter collectors material 08X18H10 steel
- Filtration frame material – food grade glass-filled
- polypropylene, tmax = 135°C , or stainless steel
- The filter lid is fixed to the filter body by means of clips to ensure easy installation and better esthetics.
- The filter is fitted with sight glasses for visual control of the filtrate quality in each filtration frame, with the possibility to shut off any of them.
- The filters are supplied with one set of filter cloth.
- Stabilization of a slurry flow entering filters with maximum pressure limit after pumps.
- Universal algorithm of filter regeneration, which can be adjusted to the specific conditions of the filtration station operation to ensure maximum filtration efficiency.
- Inverter control of pumps.
- Record of pumps service life with automatic switching to a stand-by pump at the pre-set time or in the event of a fault.
- Pumps and actuators alarming and control of operation based on limit switches.
- Process signalling of deviation of process parameters from pre-set limit values.
- Record of process parameters and data gathering and storage in the history list.
- Remote control of system regulators by using the operator’s panel or PC keyboard. Graphical mnemonic diagrams are the visual depiction of data about the technological process, equipment condition, operating modes and emergencies.